An ice machine is not like a fridge, why?
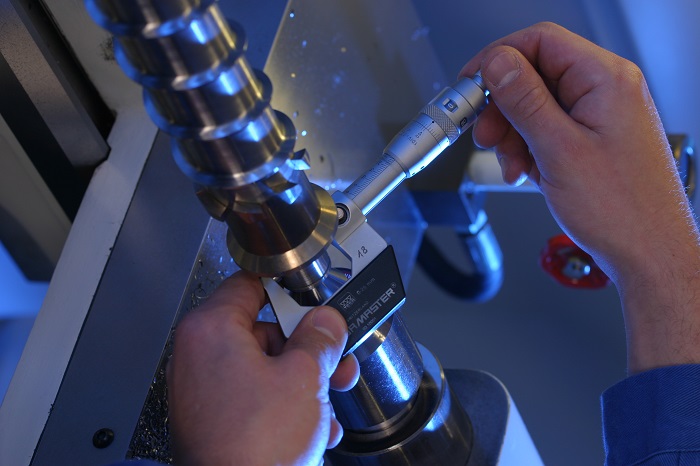
When it comes to service, ice machines cannot be compared to any other piece of refrigeration equipment, as they have to deal with much higher mechanical loads. As a result the service requirements are markedly different.
To undestand this, we have to first understand how the freezing units are made and why they are made in this way. This is necessary to apprieciate why it is important to have scheduled servicing arrangements in place to ensure that your ice machine will have a long and productive life.
The heart of all Ziegra ice machines is the freezing unit. All Ziegra freezing units are precision machined to exacting tolerances.
Each freezing unit is assembled by specialists, by hand to ensure the quality is second to none.
Preventative maintenance is the key to maximising the operating efficiency and longevity of your Ziegra ice machine, while keeping downtime to a minimum. See our Terms & Conditions for details of the service requirements for our ice machines.
During the service a Ziegra technician will strip down, clean and reassemble the freezing unit to the same exacting standards as the original assembly in the factory. All the wearable parts such as bearings and seals are replaced with new factory original Ziegra parts.
Ziegra machines should only be serviced by technicians qualified to do so using genuine Ziegra components.
As with all ice machines, as ice forms on the inside surface of the evaporator (freezing unit), the phase change from water to ice causes minerals to separate from the water and form scale which sticks to the evaporation surfaces of the ice making cylinder. This scale will be more visible when the surfaces are dry and will vary according to the type of minerals in the local water supply. As an example, lime or calcium scale can often be detected as a film that is whitish in colour, whilst iron scale can be seen as reddish brown deposits.
Scale deposits interferes with the efficient operation of your machine in three ways; firstly as the scale forms and thickens over the course of the time, it acts as an insulator and progressively reduces the efficiency of heat exchange between the refrigerant on one side of the evaporator wall and the water on the other. Secondly the surface formed is rougher and causes much higher friction than the bare evaporator wall, increasing the load on the bearings in the freezing unit and the gearbox / gearmotor. Thirdly it begins to take up the clearance between the auger and the cylinder wall, which which additionally increase the drive load. Once the cylinder reaches a certain point, the load increases exponentially resulting in very rapid component wear. Always monitor your ice machine and if you hear strange noises from the unit or notice changes to the ice quality, quantity or colour call the manufacturer for advice. All new Ziegra flake and nugget ice machines are supplied with an external water filtration system to help mitigate the effects of scale and helps to slow down wear between service intervals.
Maintaininng your ice machine under a Ziegra Service Contract takes all the hassle away, as the Ziegra service department take care of the record keeping and scheduling of your service arrangements for you. This also takes care of the F-Gas requiremets for machines with a refrigerant capacity that requires records to be kept of losses.
Also all our service contract customers receive 15% discount on all parts.
For more information about our service contracts, please use this link to CONTACT us.